To create strong and reliable electrical connections special combs are used. Let's discuss what terminal blocks are for connecting wires, what they are, as well as how to use them and install them on a din rail with your own hands.
A terminal block, screw terminal, or terminal block is a special device that is used to connect electrical wires, it is much safer than twisting. They are mainly needed so that you can tighten the wiring cables without damaging them.
Photo - Connection of terminal blocks on a DIN rail
The cable can be fastened directly under the screw head, or force-tightened with a plate and screw connection (hence the name), for more complex or delicate fastenings, pipe and screw technology is used. This device is very convenient in that it can be used to create a completely sealed wire connection, while not damaging its contacts. For special cases, the cable can be inserted either into a special lug of the terminal block, which is then inserted into the terminal or electric cabinet, or attached to the connecting tips, which in turn are fixed under the screw head. Such electrical devices are called walk-throughs.
Photo - Ground-zero terminal block
Terminal types
Depending on the design, there are such terminal blocks for cables:
- flat;
- Phillips ("screwdrivers");
- Hexagonal;
- In addition, there are bolted, spring, screwless and screw terminals for cable.
Photo - Types of terminal blocks
Screw self-clamping terminal blocks (Weidmüller, AVK Klemsan) are widely used in electrical wiring, in junction boxes, for fixing the contacts of an auto-battery, socket, light switch, connecting groups of lamps according to a certain scheme or telephone wires, installing powerful equipment (here it is necessary to use special power pads), etc.
Photo - Self-clamping screw terminal blocks
Screw terminals are commonly used to connect ground circuits, such as on a turntable or surge protector. Often, such current terminal busbars are used to protect the speakers of warning devices - acoustic systems, alarm systems, etc. Ground terminals often have a green screw and are used in household appliances, where they are equipped with "teeth" - a special grip on wires.
Photo - Grounding terminals
Video: types of terminals
Design Description
The most popular are the so-called barrier clamp terminal blocks. They are equipped with a number of short metal strips, which are separated by an insulating layer. Each wall of these terminal boxes is equipped with several screws, thanks to which the wires are securely fastened without touching each other. It is this terminal block that is most often used in electrical distribution cabinets.
Photo - Barrier clamp terminal blocks
There are also universal terminal blocks (PHOENIX CONTACT, Ensto, sv 15) for contacts that are mounted on printed circuit board, they have a simpler design. They can be characterized as an insulating block in which metal tubes are connected by a pair of clamping screws. Each end of such a tube is capable of holding wires, which is very convenient for branching wiring. They are often used to connect lighting fixtures or create street lighting(illuminations).
Photo - PHOENIX terminal block
There are also junction boxes with terminal blocks (Nevski Plastex, TB) with several screw connections along one or two metal strips, for example, ABB combs. Such a panel allows you to create a convenient device to distribute the current between the conductors.
When choosing terminal blocks, it is very important to calculate the correct pitch. This is one of the most important characteristics of supports. This indicator depends on the cross section of your wire, consider the data for the AWG cable:
Description of terminal block materials:
It should be noted that electrical tips are made of different materials to be selected based on your needs. For example, it is unacceptable to connect copper, aluminum cables different types adhesions - this can cause short circuit. In order to fasten the wires, it is best to use the same material from which they are made. For example, a copper cord will be perfectly tightened by power terminal blocks from Wago (Vago), in which the main material is copper. The same is required for aluminum, stainless steel and their alloys.
Photo - Copper terminal blocks
There are universal carbolite terminal blocks, they are able to work with any type of wire, although their price is slightly higher than special ones. The most difficult situation is if you need to connect the power wires. Each terminal material has its own performance indicators, carbolite begins to melt at a temperature of 150 degrees. Under extreme conditions, a ceramic terminal block is simply indispensable, very good reviews about the brands Legrand, Degson.
Photo - Carbolite terminal blocks
Mounting terminal blocks on a DIN rail does not take much time even for novice electricians. Many companies provide their customers with devices with an automatic latch or “tongue”, for familiarization, just look through the company’s catalog, where the technical characteristics of the panels fit you.
Photo - How to connect a terminal block to a DIN rail
First you need to calculate the number of terminal blocks. The designation of the terminals M6 / 8 indicates that we have a device with a screw pitch of 6 and a width of 8 mm, respectively, by performing simple mathematical calculations, you can calculate the required length of the DIN rail and the dimensions of the cabinet. All terminal blocks are very easy to connect to each other, for this you need to put them with the right side to each other and gently press until they click.
Now, having fixed the terminal blocks between each other and installing them on the rail, we bring to the structure electric wires. We recommend, depending on where the type of cable is and where it goes (to the board, light, stove, etc.), mark them as in the photo with a color or number. At the end of the work, we check the connections, if necessary, treat them with corrosion paste (for example, if the unit is on the street) and use it.
Photo - Designation of terminal blocks
Regardless of whether you connected the neutral wires or not, it is very important to fasten them with a fuse - this will save you and your equipment from unexpected power surges.
In addition to the described option for connecting terminal blocks, you can also buy ready-made combs right away, which you just need to snap onto the din rail.
Photo - terminal blocks
Price overview
Connecting terminal blocks can be bought at any electrical store in Russia, Ukraine, Belarus and other countries. Naturally, when buying in bulk, the price will be much lower. The cost mainly depends on the pitch and material of the terminal block, as well as the manufacturer and type of location (corner, end, etc.). The price of domestic devices is much lower than for imported ones.
For example, we suggest considering how much DEGSON plug-in terminal blocks cost for a screw with a wire cross section of 1 mm in different cities of Russia and Ukraine:
Terminal blocks are sold both in specialized stores and centers, and in markets. Be sure to check the quality certificate of the series and GOST fixtures before buying. From domestic analogues, we can recommend IEK (IEK), ZVI and ZNI.
By modern rules PUE of the 7th edition is allowed to use four methods to connect electrical wires:
Let's take a closer look at each of these connection methods.
1. Terminal connections
It is correct to use Wago clamps when branching zero and phase cores. For a branch from the protective earth conductor (PE), a different type of clamp must be used, because the main core should not be torn, which cannot be done in the Wago clamp. For this purpose, for example,
knife type clamp. About them a little lower.
Screw type terminal blocks
Terminal blocks
Screw-type terminal blocks are available for connecting electrical wires of different diameters. They are not used for connecting stranded electrical wires, if they are not crimped with brass lugs. The number of conductors clamped simultaneously is no more than 3. The wires for the connection are stripped of insulation to a distance sufficient to clamp under both screws.
During installation copper wires in junction boxes, such terminals are convenient because the connection is compact, it is easy to place it in the mounting box. However, due to the rigidity of the copper conductors, when the terminal is laid in the mounting box, a non-contact may appear in the connection. In this case, Wago clamps are preferable.
Screw terminal block for DIN rail.
On the terminal block we read the conditions of use
Another disadvantage of screw terminals is that they must be subjected to an annual audit, i.e. twist once a year, and Vago clamps serve for at least 30 years without additional maintenance.
When connecting lived from different materials for each screw, the terminals are passed through one conductor, preventing their direct contact. The reliability of such a connection, where only one screw is used to fasten each wire, is much less than when using the Wago clamp.
If it is necessary to connect conductors from different materials, then this can be done using a conventional nut, screw, grover washer and an additional washer between the conductors to exclude their direct contact:
One of the types of wire connections made of dissimilar metals
To switch Zero (N) and Earth (PE) in the switchboard, tires with screw terminals are used:
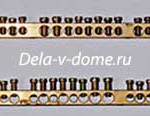
Tires in a shield. Left-RE, right-Zero.
In addition to the shield, an additional PE busbar can be placed at the point of branching into sockets, i.e. in the rooms, the kitchen, by installing a separate box for it.
Knife Terminal Connectors
Used for cutting into carrier wire branches. Both wires can have the same diameter, but more often the carrier has a larger one. With the help of connectors of this type, branches are made to sockets from an inextricable PE earth core. The braid at the insertion point does not need to be removed either from the carrier core or from the branch one. The knife cuts through the braid. To secure the latch to the knife-type clamps, it is sometimes necessary to use pliers to cut through the wire insulation. The connection is reliable and compact.
2. Connection caps, PPE
If electrical wires from dissimilar materials are connected only with the help of terminals, then wires from the same material can be switched, in addition to the terminals, also with insulating caps, otherwise PPE - connecting insulating clamps.
They come in different diameters different color and forms. Made of plastic with a steel spring screwed on the inner cone. Inside, some types of caps are filled with gel from the oxidation of wires.
Caps are used to connect and insulate both stranded and single-core wires from the same material, because. in them, the wires have direct contact, which is not allowed with dissimilar wire materials.
To connect the wires, they are stripped of insulation to a distance slightly less than the length of the cap, then folded together and twisted with a cap. The last turns for reliability must be turned with pliers.
The caps indicate the total diameter of the connected wires. This must be taken into account when choosing a cap, because. otherwise there will be no reliable connection.
3. Connections by welding
The most reliable way to connect wires is by welding. Wires should be welded from only one material, either only copper or only aluminum. Welding technology is simple, but the question arises of purchasing welding machine and certain work experience.
The wires are cleaned of insulation, they are twisted, followed by cutting off the end to an equal length of each wire. And only then is the end welded. At the end, a small ball of molten metal is formed.
It is necessary to isolate the bare ends of the wires.
The welding connection is compact, reliable in operation and durable. The connection easily fits into the junction box and does not lose contact when placed in it.
4. Branch clamps
Branch clamp "Nut"
Branch clamps, otherwise called "Nuts", allow you to make branches from the carrier core. Most often used outside the apartment and house due to the large working diameters of the wire.
To connect to the carrier core of the branch, this core is stripped to a distance equal to the length metal plates, the branch wire is also cleaned. Both wires are laid in the grooves of the plates and tightened with screws.
Compress content
Dissimilar wires can also be connected with similar clamps, i.e. copper and aluminium.
All other compounds that are still used in everyday life and even in some places in production, namely: twisting, twisting followed by soldering, according to modern rules, PUE are not allowed.
By the way, also interesting:
In the process of performing electrical wiring, each master necessarily faces such an occupation as connecting sections with a wire to each other. The most common wiring problem is a short circuit. Also, a very frequent unpleasant phenomenon is a circuit break, most often it happens at the junction of the wires. These connections are made in and mounted in the plane of the wall or on its surface. Often inside these boxes are wire connections that lead to the automatic switchboard, as well as wires that go to sockets and fixtures. In parallel, they can be laid another wire that connects the boxes together. Connections of this kind are always made strictly identical to the design schemes.
Below are the most common types of connections:
- With the help of twisting and further.
- With the help of nuts.
- With terminal blocks.
- With WAGO spring terminals.
- By connecting nulls with connecting tires.
- With bolted connections.
- By using .
Terminal blocks
The use of this switching option is the most popular due to the minimum labor costs for installation and compliance with all standards. A separate advantage is the ability to connect wires of different sections and materials. These days, the electrical materials market is overflowing with various products, but these terminal blocks are undoubtedly the best sellers.
Types of terminal connections of wires
Terminal clamps allow you to exclude the contact of wires from different materials in the connection of wires. To date, leaders in the field of electrical connections are 3 types of terminal blocks:
- Spring type.
- Screw type.
- Knife type.
Pads are mostly made of brass. They consist of assemblies of 2 or more terminals. Separate varieties are filled with a specialized gel to protect against corrosive effects from the outside. They differ from each other by: the diameter of the connecting wires, voltage and current strength.
Currently, this type of wire connection, like ordinary twisting, has begun to fade into the background. To ensure reliable contact at the junction of electrical wiring, specialized connecting terminals are used, which are called terminal blocks. On the modern market our country is represented by a huge variety of such pads. They differ from each other: the price tag, design and some performance features.
The pad design is identical. It consists of the body itself, inside which there are special cells, and inside these cells there are already brass tubes with several threaded holes.
The tubes themselves come in different sections, they are selected according to the diameter, according to the diameter of the section of the wires themselves.
Terminal blocks are used in a wide variety of places. An example is the way to connect an ordinary chandelier in an apartment, connect it to short conductors sticking out of a hole in the ceiling.
This method is often used to connect wires that are broken and located in the wall. Often such conductors do not have enough length for subsequent connection in another way.
Advice from the master: “The pads should be located directly in junction box. Placing them inside the plaster is strictly prohibited!”
Although this connection is inferior in its reliability to the connection, but in the end it is more convenient and requires minimal time.
The main advantage of terminal blocks is the fact that they can connect aluminum and copper conductors. To exclude the oxidation process, in this case, only one wire is passed through the clamping screws, the contact between the cores is completely excluded.
WAGO terminals. Design features and differences from other terminals.
WAGO (WAGO Kontakttechnik GmbH & Co. KG) was founded in 1951 in Germany. She began her production with the development and implementation of spring terminals, in which she was very successful. Until today, the company is engaged in the production of this electrical equipment and finds only positive feedback in the electronics and electrical engineering market.
1973 marked the beginning of the production of the first compact terminals k. Further, these products were patented, and production began to increase. Today, VAGO is the world leader in the production of spring terminals and other connectors required for electrical wiring.
The main advantages of spring terminals are:
- High level of vibration resistance of the obtained connection.
- The point of contact itself is firmly fixed, thanks to the pressure of the spring. This feature makes it possible to exclude plastic deformation of the metal.
WAGO wire terminal blocks have passed all kinds of international wiring certifications. They can be used when reconnecting wires. Also, the terminals are equipped with technological holes for connecting the probe to a thin carrier rail. Products do not require the use of special tools.
The terminal group includes both springs and thin-bearing rails. These tires are made by tinning copper. This fact provides protection against corrosion and increases the contact area of the cores.
The springs are flat and made of austenitic steel. Due to this, they have increased elasticity.
The housing for these terminals is electrically insulating. It is made from modified polyamide and polycarbonate. These substances are highly resistant to ignition, self-extinguishing, resistant to fuels and lubricants and other external influences.
Connecting wires using terminal blocks
Choosing a block for connecting wires is a responsible action. It is necessary to pay attention to the strength of the current that will subsequently run through this product. It is also necessary to purchase the required number of mounting terminals.
The process itself is not a complicated procedure, even amateurs can carry it out with the initial necessary knowledge and skills.
The block is selected according to the size of the cell, all unnecessary sections are cut off. Most often they make terminal blocks.
Having previously removed the conductors from the connecting ends, the cores of the wires are inserted into the terminal cells and all conductors are clamped with screws. The surface of the core must be cleaned. A small amount of force is allowed when tightening the screws.
In the case of connecting aluminum conductors, the screws are tightened very carefully, without much pressure. This is done to avoid breaking the wire and worsening the contact in the future, since this metal has a high fluidity when heated strongly.
Advice from a specialist: "Knots and assemblies in which aluminum compounds are present must be tightened every year."
Conclusion
Having a good and reliable contact depends on the choice of quality Supplies and competent production of the operation itself. It is worth paying attention to the stability in the work of the entire electrical circuit, equipment connected to it and other systems. Only quality work done on the connection electrical wires and knowledge of the necessary standards, will be able to eliminate various troubles with electricity and work electrical appliances further.
If someone still believes that there is nothing better for connecting wires than stripping their ends with a knife, twisting them, and wrapping them with electrical tape, then he is behind the times. Today there are already a lot of alternative devices that greatly facilitate the process of connecting wires, and at the same time are quite reliable. Times will soon sink into oblivion, because they are being replaced by a variety of terminals.
Why are clamps good? How, for example, to make the connection reliable and durable?
It is categorically impossible to twist copper with aluminum, because then a galvanic couple is formed, and corrosion will simply destroy the connection, and it doesn’t matter how much current passes through the twist, it will collapse sooner or later, and if the current is higher, switching on and off devices more often, then the twisting resistance will increase faster, over time, the heating of the twisting point will become more and more.
In the end, this is fraught with a fire, or at best - the smell of melted insulation. The terminals in this situation would have saved, and it would not have come to the destruction of the place of contact.
The simplest solution is to put . Polyethylene terminal blocks are sold today in every electrical store, and are not expensive. Inside the polyethylene frame, several brass tubes (sleeves) are arranged in a row, in which the ends of the connected wires are clamped with two screws. If desired, you can cut off as many tubes in polyethylene as you need, and connect as many pairs of wires as you need.
However, not everything is so rosy, aluminum flows under the pressure of the screw at room temperature, so periodically, once a year, it will be necessary to tighten the connection. Otherwise, if it comes to connecting copper conductors, everything will be in order.
If you do not promptly tighten the staggering in the terminal block aluminum wire, then the end of the wire that has lost its former contact will spark and heat up, and this is fraught with a fire. It is impossible to clamp stranded wires into such a terminal block without auxiliary pin lugs, which we will talk about later.
If you just squeeze stranded wire into such a terminal block, then the pressure of the screw on the thin wires, combined with rotation and uneven surface, will cause some of the wires to become unusable, and this threatens to overheat. If the stranded wire fits tightly along the diameter of the sleeve, this is the most acceptable connection option, because there is less risk of a broken connection.
As a result, we can conclude that polyethylene terminal blocks are good for single-core, and only for copper wires. If you want to clamp a stranded one, you will have to put on an auxiliary lug, which will be discussed later.
The next convenient option connecting terminals- . Such terminal blocks are also equipped with transparent covers that can be removed if desired. Fastening is very simple: the stripped end of the wire is inserted between the pressure and contact plates, and pressed with a screw.
What are the advantages of such terminal blocks? Firstly, unlike polyethylene terminal blocks, plastic terminal blocks have an even steel clamp, there is no direct pressure of the screw on the cores. The clamping part has a recess for the wire. As a result, these terminal blocks are applicable for connecting groups like. Why groups? Because this terminal block can not be cut like polyethylene.
Next - self-clamping terminals, an example of which is. These are express terminals for fast, one-time wiring. The wire is pushed all the way inside the hole, and there it is automatically fixed by a pressure plate that presses the wires against a special tinned bar. The clamping force is maintained all the time, thanks to the material of the clamping plate.
These express terminals are disposable, but in principle you can pull out the wire by gently rotating it while pulling it out. But if you pull out the wire, then it is better to make the next connection in a new clamp, fortunately, they are not expensive, 10-20 times cheaper than terminal blocks.
The inner copper plate is tinned, and allows you to fix even aluminum, even copper wires. The clamping force is maintained continuously, and the wire does not have to be pressed once a year, as is the case with terminal blocks.
Inside there is also a lubricant based on quartz sand with technical petroleum jelly, for an abrasive, removing oxide film on the surface of the wire, preventing, thanks to petroleum jelly, its reappearance. These express terminals are transparent and opaque. In any case, plastic does not support combustion.
Suitable for connections with prospective current up to 25A. Terminals from other manufacturers may suffer from heat, such as weakening the clamping force of the spring contacts, so use only branded, well-proven terminals.
Suitable as reusable terminals. These are terminal blocks with lever clamps. You can also clip wires here. various types. The fastening process is simple: the lever is raised, the end of the clamped wire is inserted, the lever is pressed - fixation occurs.
This clamp is reusable. When the lever is raised, the fixation is removed, you can pull out one wire and insert another. This terminal type is ideal for multiple reconfiguration of conductor groups. Withstands currents up to 32 amps without overheating. The design of the clamp is a bit similar to a one-time express clamp, the difference is again in the possibility of repeatedly switching the connected conductors.
Let's consider next. These are disposable connectors for low current wires. Using adhesive tape, you can connect telephone wires, low-power LED lights etc. The essence of this fastener is a mortise contact.
Several wires, right in the insulation, are inserted into the sleeve, then crimped with pliers. Structured cabling installers love scotch locks. Scotch locks allow you to connect wires without having to strip them. The plate with cutting contacts simply cuts into the insulation, and comes into contact with the conductor, with the core.
Scotch locks come in two and three cores. The peculiarity of such terminals is that they are cheap, waterproof, versatile, and do not require stripping the ends, but are crimped with simple pliers. Inside the coupling there is a hydrophobic gel to protect the contacts from moisture and corrosion.
If it is necessary to replace the connection, the adhesive tape is simply cut out along with pieces of wire, and a new one is put in.
When you need to connect several wires into one powerful knot, for example, just combine them, or for laying on a terminal block, use cartridge cases. Sleeves are used most often universal, these are usually tinned copper sleeves in the form of tubes, or in the form of flat tips with a mounting hole.
The wires are inserted into the sleeve, and crimped with a special tool - a crimper. Crimper- this is . The great advantage of the sleeves is that such crimping does not create increased resistance at the junction. Sleeves in the form of a flat tip with a hole are convenient when you need to fix a wire or a bundle of wires to the body with a screw. Simply select a sleeve of a suitable diameter, crimp it, and attach the tip to where you need it.
To connect stranded wires, to combine solid wires with stranded wires, or simply to fix them in terminal blocks, they are used.
The stranded wire is conveniently inserted into the lug, the lug is crimped together with the wire, after which the stranded wire can be fixed in any terminal block, even in polyethylene, without fear that the connection will be broken.
The decisive factor here is right choice the diameter of the tip, it must correspond to the total diameter of the crimped, combined into a bundle, lived, so that the wires do not pop out later.
To crimp the pin lugs, you can do with pliers or use a screwdriver and a hammer.
Terminal block- This is a special wiring device for connecting conductors. Any block consists of a pair (or several pairs) of metal contacts with fasteners for conductors, which are located in a dielectric housing.
They have a number of advantages:
- Ease of use.
- Connectivity wires from dissimilar materials.
- Corrosion protection and other external influences.
- Reliability, the strength of the joints.
Terminal blocks can have a different design. The most popular are 3 types of execution:
- screw;
- spring;
- knife;
Screw type terminal blocks
Screw terminals- one of the most common types. They are a brass sleeve with two bolts in a plastic case. Contact is provided by bolt pressure. The case can be made of different materials - polyethylene, polyamide and polypropylene. With their help, you can connect wires with a cross section from 0.5mm 2 to 35mm 2.
The advantages of screw pads include:
- Not required special tool (only a screwdriver is needed).
- Possibility multiple use.
- Possibility using the required number of segments.
Screw pads also have a number of disadvantages:
- High transition resistance.
- Low reliability(weaken with vibration).
- Restrictions by wire material.
- Installation duration.
- Required a certain skill for puffing.
- Necessary annual service.
Such terminals are undesirable. They have increased "fluidity", the connection weakens over time. To avoid heating due to an increase in contact resistance, they must be regularly tightened. This creates inconvenience during operation.
Certain problems arise with stranded wires. It is possible to perform high-quality installation with screw connections only using special tips or pads with a pressure plate. Otherwise, there is a possibility of damage to the cores when tightening the screw.
Thus, solid copper wires are most suitable for this design.
Mounting with a screw connection is very simple:
- From pads cut off the required number of terminals (with a regular knife).
- strip the insulation connected wires (by 5-12mm).
- Insert stripped wire ends into terminals;
- Tighten the screws.
Dealing with this is easy. The main thing is to be careful when tightening the screws and choose high-quality terminal blocks.
When choosing, special attention should be paid to the manufacturer of the product. Today, there are products of different brands on sale. It is better to use products from such well-known manufacturers as Legrand, ABB, Tridonic, Werit.
Prices for products depend not only on specifications, but also from the manufacturer:
Spring Type Terminal Blocks
The most common blocks of this type are self-clamping terminal blocks from WAGO.
The WAGO series is available in 2 versions:
- PUSH WIRE(one-piece disposable).
- CAGE CLAMP(reusable).
It is impossible to remove the conductor from disposable terminals without damaging the terminal block. Reusable have a convenient lever to release the conductor.
This equipment is widely used not only in industrial production, but also in domestic conditions. They are especially popular for lighting networks.
Clamping occurs with the help of a steel spring coated with a special chromium-nickel alloy. The intricately shaped spring provides a reliable, durable connection. The case, made of polycarbonate or polyamide, can withstand a wide range of temperatures, resistant to aggressive environments.
The terminal blocks themselves are made of tinned copper. This significantly increases the contact patch, reduces contact resistance, and protects against corrosion. In addition, WAGO can be filled with a special lubricant that provides additional protection from corrosion.
WAGO model
WAGO is capable of connecting 2-8 conductors with a diameter of 0.5-4mm2. They are designed for a nominal voltage of 220V and a current of 32A.
All springs come in 2 versions - for a DIN rail and a regular version.
Under the DIN-rail, terminal blocks are used in control panels and control cabinets, distribution boxes. They are used wherever there is increased vibration (for example, machine building, railway industry).
Phoniexcontact manufactures DIN rail terminal blocks for wires with and without ferrules up to 35mm2. It is possible to connect up to 50 wires at the same time.
The main advantage of Phoniexcontact equipment is its versatility. You can do any assembly. All elements are easily docked with each other.
Installation is extremely simple and accessible:
- First you need to prepare the conductor - strip the insulation by about 10-13mm.
- For wire connection it is enough to open the clamp with a conventional screwdriver, insert the conductor and remove the screwdriver. The contact will close automatically.
Advantages of spring connections:
- Availability separate socket for each conductor.
- Strong, high quality connection.
- Low transitional resistance.
- Possibility joining wires from various materials.
- Corrosion protection and other external influences.
- Not required special tools.
- Not required special skills.
- Possibility reusable application.
- Does not require annual service.
- Sustainability to vibrations.
- Free access for measuring instruments.
- Potential distribution(if necessary) using jumpers.
The disadvantages include not high permissible currents.
In addition to these famous brands, such as WAGO, Phoniexcontact, similar equipment is produced by Legrand, ABB.
Table:
Manufacturer | Type of | Characteristics | Price, rub |
WAGO | 222-412 | 2x0.08 - 4mm2, 32A, copper | 15,80 |
WAGO | 222-415 | 5x0.08 - 4mm2, 32A, copper | 31,50 |
WAGO | 273-248 | 8x0.5-2.5 mm2, 24A, copper/aluminum with Alu-Plus paste | 21,70 |
WAGO | 273-503 | 3x1.5-4 mm2, 32-24A. copper/aluminum | 34,10 |
Phoenixcontact | ST 1.5 - 3031076 | Feedthrough, 0.08-1.5mm2, AWG 28 - 16, Width: 4.2mm, 17.5A | 22.97 |
Phoenixcontact | SP 2,5/ 1-L 3043019 | Plug-in, 1 pole, 0.08 mm2 - 4 mm2, AWG: 28 - 12, Width: 5.2 mm, Height: 39 mm, 24A | 91.59 |
Blade terminal blocks
Such pads are used much less frequently. Mainly for grounding and grounding circuits when mounted with an inextricable conductive conductor. They are used to cut branches into a carrier conductor.
In addition, knife connections are widely used in audio technology. Blocks are produced with a width of 5 mm for conductors 0.2 ... 1 mm2, a width of 6 mm for conductors 1 ... 2.5 mm. A large contact area allows you to withstand currents up to 24A. The color scheme is quite diverse: yellow-green, orange, gray, blue and red.
There are disposable and reusable pads.
Scotchlok disposable model
Disposable pads include Scotchlok pads, which are manufactured by 3M. In them, the joining of several wires is carried out by pressing with a special tool.
Their main distinguishing feature – during installation, stripping of the conductor is not required. The wire, together with the insulation, is inserted into the terminal block and crimped until it is completely fixed. The insulation is cut through with contacts, providing a reliable one-piece connection.
Advantages of knife terminal blocks:
- Time saving for installation.
- Stripping and crimping wires are not required.
- Secure connection by means of a lever with a latch.
- Reliability, compactness.
- Not required special tool.
- Not required Special Skills.
- Increased electrical safety.
The only downside is the high price.
Products are manufactured by such well-known manufacturers as Klemsan, Legrand, 3M, and many others.
Table:
Manufacturer | Type of | Characteristics | Price, rub |
3M | 7000031438Scotchlok | 1.5-2.5 mm2 | 14.36 |
3M | 7000031482 Scotchlock | 3x(0.5-1.5mm2) | 38.30 |
3M | 7100003139 Scotchlock | 2.5-4.0 mm2 | 17.78 |
General installation requirements
The quality of connections and branches during installation is of paramount importance. When troubleshooting an electrical circuit, most often the problem occurs due to a lack of contact. Poor contact can lead not only to a circuit break, but also to overheating of the wires. Often this is the cause of a fire.
Therefore, they are subject to stringent requirements.
Regardless of which terminals are installed, the following rules must be observed:
- During installation it is necessary to leave a margin of wires in front of all connections (for reconnection).
- All connections should be in accessible locations.
- Location of connecting elements must be protected from vibration and any other mechanical influences.
- Insulation connecting elements must match the insulation of the conductors.
- All connections must be carried out in cabinets and control panels, special niches of building structures.
There are many varieties of terminal blocks for their intended purpose:
- plug-in;
- hybrid;
- mini and micro terminals;
- fuse terminals;
- terminals with breakers;
- multi-output;
- multi-tiered;
- checkpoints and others;
For all varieties, the installation rules are the same.
- With high vibrations use of spring terminals is recommended.
- Screw pads with pressure plates are more reliable than conventional ones.
- All connections aluminum wires require pulling at least once a year.
- It is not allowed to place terminal blocks in plaster. They must be hidden in the junction box.
- Inserting the wire into the block must be done before the insulation layer.
- After installation, you need to check the quality of the connection by lightly pulling the wire from the terminal block.